Why the Shell & Tube Heat Exchanger Remains the Backbone of Industrial Heat Transfer
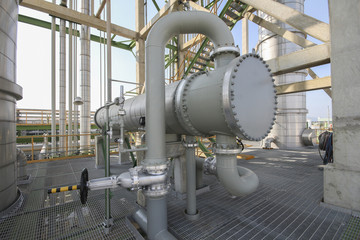
In the landscape of industrial heat switch, no factor stands taller than the Shell & Tube heat exchanger. With decades of established overall performance and adaptability, it has earned a place in strength flowers, refineries, chemical centers, and HVAC systems worldwide. Characterized by its cylindrical shell enclosing a series of tubes, this tool is designed to successfully alternate heat among fluids—one flowing inside the tubes and the opposite outdoor but inside the shell. Its robustness beneath strain, modularity, and efficiency have cemented it as a cross-to solution across numerous programs.
Whether used to condense steam, preheat fluids, or recover waste heat, this exchanger gives flexibility this is unmatched inside the global of thermal structures. While technology including screw vacuum pumps have advanced and diversified fluid processing skills, the Shell & Tube warmness exchanger keeps its dominant position in structures in which reliability, scalability, and performance are important.
The Fundamentals of Operation
How the System Facilitates Heat Exchange
At the heart of the design is a easy yet powerful precept: shifting thermal electricity between two fluids without direct touch. The fluid in the tubes can be heated or cooled because it passes via, at the same time as the fluid inside the shell performs the opposite function. Thermal strength is exchanged via the tube walls, facilitated by using the temperature distinction among the 2 fluids. This method is continuous and optimized by developing turbulent drift to increase the fee of heat switch.
The fluids can move in parallel, counterflow, or crossflow configurations. Among those, counterflow grants the very best thermal performance through retaining a positive temperature gradient throughout the exchanger’s period.
The Role of Each Component
The shell presents the structure and containment for the shell-aspect fluid. Inside, a package of tubes consists of the tube-side fluid. Tube sheets anchor the tubes at each ends and prevent the fluids from mixing. Baffles, established in the shell, manual the flow and create turbulence to improve warmness transfer. Channel heads at either end of the shell direct the fluid into and out of the tube package deal.
Maintenance and inspection access is made feasible by detachable covers and washer-friendly surfaces, permitting these exchangers to serve reliably over lengthy operational cycles.
Industrial Applications and Their Demands
Energy Production
In the power sector, Shell & Tube warmness exchangers play an essential component in structures requiring thermal conversion. From heating boiler feedwater in fossil fuel vegetation to cooling steam in condensers, their potential to handle excessive pressures and fluctuating temperatures makes them essential in strength generation.
Petrochemicals and Refining
Oil and fuel refining depends on strong warmness exchangers to manipulate section changes and chemical reactions. Shell & Tube devices are specially valued right here for their resistance to harsh chemical compounds and compatibility with excessive-temperature fluids. This permits green crude oil distillation, gas cooling, and hydrocarbon healing techniques.
Pharmaceutical and Biotech Operations
In pharmaceutical production, temperature manipulate is crucial for product integrity and protection. The warmth exchanger supports sterilization, unique heating of reactors, and restoration of technique heat, all even as preserving strict hygiene requirements through sanitary designs and corrosion-resistant materials.
Food and Beverage Industry
These exchangers are widely used for pasteurization, fermentation, and cleansing-in-vicinity techniques inside the food sector. Stainless steel tubes make sure hygiene and withstand corrosion, at the same time as the exchanger’s modular layout lets in for instant modifications in manufacturing necessities.
Chemical Processing Facilities
The chemical enterprise makes use of Shell & Tube exchangers to regulate response temperatures, condense vapors, and appropriately switch heat among corrosive or unstable materials. Materials including titanium and Hastelloy are often used to make certain lengthy-term resistance to chemical put on and thermal fatigue.
Core Benefits of the Shell & Tube Design
Performance Under Pressure
This exchanger type excels in environments wherein both excessive pressures and temperatures are present. Its robust layout resists deformation, strain drops, and leaks, that are often issues in extra compact or light-weight warmness exchanger alternatives.
Modular Customization
No industrial techniques are equal, that's why the modularity of Shell & Tube designs is vital. Engineers can specify tube preparations, baffle configurations, and substances to suit actual method conditions, optimizing overall performance while reducing fees.
Ease of Cleaning and Maintenance
The accessibility of the tube bundle and channel heads makes it simpler to easy and check out the inner surfaces. In industries like food and chemical substances, in which fouling can speedy degrade gadget performance, this ease of preservation is a primary advantage.
Durability and Longevity
When constructed with the right substances, Shell & Tube heat exchangers can final for decades. Their mechanical simplicity reduces the wide variety of failure factors, and their ability to absorb thermal expansion guarantees fewer structural problems through the years.
Design Variables and Considerations
Tube Configuration and Size
The number, diameter, and arrangement of tubes decide the surface place to be had for heat alternate. Denser tube bundles provide extra surface place but may increase the danger of fouling. Tube period also affects the exchanger’s footprint and effectiveness.
Flow Arrangement
The choice of parallel flow, counterflow, or crossflow configurations is pushed using the preferred thermal effects. Counterflow systems are desired while maximizing heat recuperation is essential, at the same time as parallel go with the flow can be used when inlet temperatures are extra tightly managed.
Baffle Design
Baffles serve to growth turbulence and direct the glide of shell-aspect fluid throughout the tubes more than one instances. Their spacing and cut patterns have an effect on stress drop and heat transfer fees. Properly designed baffles decorate overall performance without inflicting immoderate strain loss.
Material Selection
Choosing the right materials protects the unit from chemical assault and thermal fatigue. Stainless steel is commonplace for its stability of corrosion resistance and fee, whilst exotic alloys are utilized in extreme environments. The fluids concerned, in addition to neighborhood environmental factors, play a chief function on this decision.
Common Challenges in Operation
Fouling Accumulation
Over time, particulates, minerals, or natural matter can acquire on the tube walls, lowering thermal efficiency. Regular cleansing, fluid treatment, and the use of turbulence-promoting baffles help mitigate fouling and extend device life.
Corrosion and Erosion
Chemical reactions among the fluid and creation substances can lead to corrosion, whilst excessive-pace fluids can motive erosion. Monitoring float prices and deciding on suitable substances are crucial for fending off untimely failure.
Vibration and Noise
High float velocities or improperly spaced baffles can purpose tube vibration. This not only generates noise but may also lead to mechanical fatigue or rupture. Proper design and simulation can help avoid these troubles.
Thermal Stress
When the shell and tube sides function at significantly unique temperatures, enlargement quotes can vary. This creates mechanical stress that, if unmanaged, could damage seals or welds. The use of floating heads or enlargement joints permits the additives to enlarge independently without compromising performance.
Innovation and Future Trends
Digital Monitoring Systems
With the upward push of clever production, heat exchangers are actually being geared up with sensors to screen temperature gradients, strain drops, and fouling indicators in actual time. This information permits predictive maintenance, permitting problems to be addressed earlier than they turn out to be screw ups.
Compact and High-Efficiency Designs
Advancements in material science and fluid dynamics modeling are leading to smaller, extra green Shell & Tube devices. These more moderen models offer improved performance at the same time as occupying much less area, a valuable trait in facilities in which footprint is a top class.
Sustainable Manufacturing and Operation
Sustainability is pushing the development of exchangers which can be less difficult to recycle, require much less electricity for operation, and use environmentally friendly substances. Combined warmth and electricity (CHP) structures are more and more integrating Shell & Tube exchangers to maximise power healing and reduce waste.
Integration with Vacuum and Process Systems
Modern business setups often require near interplay among warmness exchangers and vacuum systems. The integration of Shell & Tube designs with device together with screw vacuum pumps allows operations at decrease pressures, improving evaporation and condensation procedures even as improving typical power efficiency. These incorporated systems offer progressed manage and more thermal responsiveness throughout various manufacturing sectors.
Conclusion
The Shell & Tube warmness exchanger isn't always simply a piece of system; it's far a foundational element in countless commercial systems. Its reliability, adaptability, and strength beneath challenging conditions make it a critical part of operations from power generation to food processing. As technologies retain to evolve, this layout maintains to show its worth via integrating with cutting-edge structures, lowering strength waste, and standing as much as the most stressful thermal applications.
While other warmth exchanger designs may provide niche advantages, few can suit the flexibility and lengthy-term cost of the Shell & Tube configuration. As industries are looking for answers that are each green and sustainable, this workhorse of heat transfer remains a steadfast preference, evolving in line with the future of commercial engineering.
What's Your Reaction?


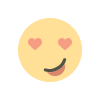
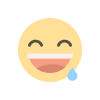


