How Does Robotic Laser Welding Reduce Material Waste in Manufacturing
Robotic Laser Welding offers precise, efficient welding solutions that reduce material waste and enhance manufacturing productivity

In today’s fast-paced manufacturing world, every company wants to improve efficiency and reduce waste. One of the most effective ways to achieve this is through robotic laser welding. This advanced technology helps industries minimize errors, save costs, and make the most of their materials. In this blog, we’ll explore how robotic laser welding plays a key role in reducing material waste in manufacturing.
What Is Robotic Laser Welding?
Understanding the Basics
Robotic laser welding is a welding process where a robot is programmed to perform precise welding tasks using a laser beam. This laser beam melts the materials, allowing them to fuse together without the need for any additional filler materials. This process can be applied to a wide range of metals, plastics, and other materials, making it a versatile solution for many industries.
Why Is Robotic Laser Welding Becoming So Popular?
Robotic laser welding is becoming more popular because of its accuracy, speed, and efficiency. It ensures that the welds are clean and precise, which reduces the chance of errors or waste. This makes it a preferred choice for industries that deal with large-scale production, such as automotive, aerospace, and electronics.
How Does Material Waste Happen in Traditional Welding?
Errors in Manual Welding
In manual welding, there is always a risk of human error. Mistakes can happen due to fatigue, lack of focus, or inconsistent handling of the welding equipment. When errors occur, it often results in wasted materials, as the damaged parts cannot be reused and must be discarded.
Inconsistent Heat Application
Traditional welding methods, especially those done by hand, can sometimes apply too much or too little heat. If too much heat is applied, the material may warp or melt, leading to wastage. On the other hand, too little heat can cause weak joints, leading to the need for repairs or even full replacements, which also contributes to material waste.
Overuse of Filler Material
In many traditional welding methods, filler materials are required to complete the weld. However, the use of too much filler material can lead to excess waste. Since robotic laser welding doesn’t rely heavily on fillers, it helps reduce the amount of material used in each weld.
How Does Robotic Laser Welding Minimize Material Waste?
Precision Welding Reduces Errors
One of the primary ways robotic laser welding reduces material waste is through precision welding. The robots are programmed to follow exact specifications, ensuring that each weld is perfect. This level of accuracy eliminates the common mistakes seen in manual welding, such as missed joints or uneven welds. As a result, there is less need to scrap or rework parts, reducing overall material waste.
Consistent and Controlled Heat Application
Robotic laser welding applies heat consistently and precisely to the weld area. The laser only heats the exact spot where the weld is needed, minimizing the risk of damaging surrounding materials. This controlled heat application prevents warping, cracking, and other issues that could result in material waste.
No Need for Filler Materials
Another advantage of robotic laser welding is that it doesn’t always require filler materials. This is because the laser melts the base materials directly, allowing them to fuse together without additional substances. By reducing the reliance on fillers, robotic laser welding helps cut down on the amount of material needed for each project.
Faster Production with Less Scrap
Robotic laser welding systems work at a much faster rate than manual welding. This means that more parts can be produced in a shorter amount of time, with fewer errors. Because the welding process is so efficient, there is less need to stop production due to mistakes, and fewer parts are scrapped. This not only saves time but also reduces the waste of valuable materials.
Benefits of Robotic Laser Welding in Reducing Waste
Improved Accuracy and Precision
One of the biggest benefits of robotic laser welding is the improved accuracy it offers. The robots can be programmed to create exact welds with little room for error. This means that parts are more likely to be welded correctly on the first try, which reduces the need for reworking or replacing parts. When fewer parts are scrapped, less material is wasted.
Reduced Material Costs
By minimizing errors and waste, robotic laser welding helps reduce overall material costs. Companies don’t need to purchase as much raw material because there is less waste. Over time, these savings can add up, making robotic laser welding a cost-effective solution for manufacturers.
Better Use of Resources
With robotic laser welding, manufacturers can make better use of their resources. Since the process is more efficient and precise, fewer materials are wasted, and more parts can be produced from the same amount of raw materials. This leads to higher productivity and less environmental impact.
Lower Environmental Impact
Reducing material waste not only benefits a company’s bottom line but also helps the environment. By using fewer raw materials and reducing the amount of waste produced, manufacturers can lower their environmental footprint. Robotic laser welding contributes to this by ensuring that materials are used efficiently and that less waste ends up in landfills.
Examples of Industries Benefiting from Robotic Laser Welding
Automotive Industry
In the automotive industry, precision is crucial. Robotic laser welding is commonly used to weld components such as car frames, exhaust systems, and engine parts. The ability to create strong, precise welds helps manufacturers reduce material waste while maintaining the quality of the final product.
Aerospace Industry
In the aerospace industry, where safety and reliability are top priorities, robotic laser welding is used to create lightweight, high-strength components. By reducing the need for reworking or scrapping parts, robotic laser welding helps aerospace manufacturers save both materials and time.
Electronics Industry
The electronics industry also benefits from robotic laser welding, especially in the production of small, delicate parts. The precision of robotic laser welding ensures that these parts are welded without damaging the surrounding material, reducing the risk of waste.
How Can Companies Implement Robotic Laser Welding to Reduce Waste?
Invest in Robotic Laser Welding Systems
For companies looking to reduce material waste, investing in a robotic laser welding system is a smart move. While the initial investment may be high, the long-term savings in materials, time, and labor make it worthwhile. Many manufacturers find that the system pays for itself over time by reducing waste and improving efficiency.
Train Employees to Operate the System
Even though robotic systems handle the actual welding, employees still need to be trained to operate and maintain the system. Proper training ensures that the robots are programmed correctly and that the welding process runs smoothly. This further reduces the chances of errors and material waste.
Monitor and Optimize the Welding Process
To get the most out of robotic laser welding, companies should continuously monitor and optimize the welding process. By analyzing data from the system, manufacturers can identify areas where improvements can be made, further reducing waste and increasing efficiency.
Conclusion
Robotic laser welding is a powerful tool for reducing material waste in manufacturing. Its precision, speed, and efficiency make it an ideal solution for industries that want to minimize errors and make better use of their materials. By investing in this advanced technology, manufacturers can save money, reduce their environmental impact, and improve overall productivity. As more companies adopt robotic laser welding, we can expect to see even greater improvements in material efficiency and waste reduction across the manufacturing industry
For more insightful articles related to this topic, feel free to visit fresnonewspost.com
What's Your Reaction?


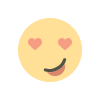
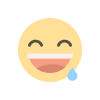


