Agitated Thin Film Evaporators in the Chemical Industry: Innovations and Sustainability
An Agitated Thin Film Evaporator (ATFE) is a specialized type of heat transfer device designed to concentrate, distill, or separate components in liquid mixtures.

What is an Agitated Thin Film Evaporator (ATFE)?
An Agitated Thin Film Evaporator (ATFE) is a specialized type of heat transfer device designed to concentrate, distill, or separate components in liquid mixtures. It is characterized by a rotating wiper system that creates a thin film of the liquid on the heated surface, facilitating efficient heat and mass transfer. The design ensures minimal residence time and prevents thermal degradation, making it ideal for processing heat-sensitive or viscous materials.
ATFEs are widely used in industries such as chemicals, pharmaceuticals, food processing, and petrochemicals. Their unique ability to handle high-viscosity materials and operate under vacuum conditions enhances their versatility and efficiency, distinguishing them from traditional evaporators.
How ATFEs Operate and Their Efficiency in Chemical Processes
How Agitated Thin Film Evaporator Operate ? involves feeding the liquid into a cylindrical chamber with a heated surface. A rotating wiper mechanism spreads the liquid into a thin, uniform film, exposing it to the heated surface. As the liquid film is heated, the volatile components vaporize and are collected through a condenser, leaving behind the concentrated residue.
Key factors contributing to ATFE’s efficiency include:
-
Thin Film Formation: This maximizes heat transfer while minimizing thermal degradation.
-
Low Residence Time: The short exposure to heat prevents the breakdown of sensitive compounds.
-
Vacuum Operation: Reduces the boiling point of the liquid, further protecting heat-sensitive materials.
-
Scalability: ATFEs can handle a wide range of throughputs, from laboratory to industrial scales.
This efficiency makes ATFEs indispensable in processes like solvent recovery, distillation of high-boiling-point substances, and the concentration of thermally unstable materials.
Innovations in Agitated Thin Film Evaporators
Recent advancements in ATFE technology have focused on improving performance, energy efficiency, and adaptability to new challenges in the chemical industry:
-
Enhanced Wiper Designs: Innovations in wiper materials and geometries have improved the uniformity of film distribution, reducing fouling and maintenance needs.
-
Material Improvements: The use of advanced alloys and coatings enhances corrosion resistance and extends equipment life.
-
Digital Monitoring: Integration of IoT and advanced sensors allows real-time monitoring of parameters like temperature, pressure, and film thickness, enabling predictive maintenance and process optimization.
-
Hybrid Configurations: Combining ATFEs with other technologies, such as falling film evaporators, has broadened their application scope and improved energy efficiency.
Sustainability in Agitated Thin Film Evaporators
Sustainability is a growing priority in the chemical industry, and ATFEs contribute significantly to achieving eco-friendly operations:
-
Energy Efficiency: The optimized heat transfer and vacuum operation reduce energy consumption compared to conventional evaporation systems.
-
Minimized Waste: The precise separation process ensures higher recovery rates of valuable products, minimizing waste generation.
-
Reduced Carbon Footprint: By enabling the recovery and reuse of solvents and other materials, ATFEs support circular economy principles.
-
Durability and Longevity: Enhanced materials and designs reduce the need for frequent replacements, conserving resources.
Applications of Agitated Thin Film Evaporators in the Chemical Industry
ATFEs find extensive applications in the chemical industry due to their versatility and efficiency:
-
Solvent Recovery: Recovering and purifying solvents for reuse in chemical processes.
-
Distillation of High-Boiling Substances: Efficient separation of components with close boiling points or high boiling temperatures.
-
Concentration of Viscous Solutions: Processing polymer solutions, resins, and adhesives.
-
Purification of Heat-Sensitive Compounds: Purifying vitamins, essential oils, and pharmaceuticals without degradation.
-
Waste Treatment: Reducing and concentrating waste streams for easier disposal or further processing.
Future Trends and Outlook
The future of ATFEs in the chemical industry looks promising, driven by advancements in technology and a focus on sustainability. Key trends include:
-
Customization: Tailored designs to meet specific industry requirements and process challenges.
-
Automation and AI Integration: Smarter systems with machine learning capabilities for predictive maintenance and process optimization.
-
Green Chemistry Applications: Supporting eco-friendly processes by enabling energy-efficient and waste-reducing operations.
-
Global Expansion: Increasing adoption in emerging markets, where demand for efficient chemical processing solutions is rising.
Conclusion: Agitated Thin Film Evaporators in the Chemical Industry
Agitated Thin Film Evaporators have cemented their position as indispensable tools in the chemical industry. Their ability to handle complex separation and concentration tasks with efficiency and minimal environmental impact aligns with the industry's goals for innovation and sustainability. As technology continues to evolve, ATFEs are poised to play an even more critical role in shaping the future of chemical processing, offering a pathway to greener and more efficient operations.
What's Your Reaction?


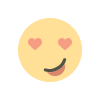
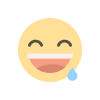


